Inner Layers Etching Process: "Acid" Etching
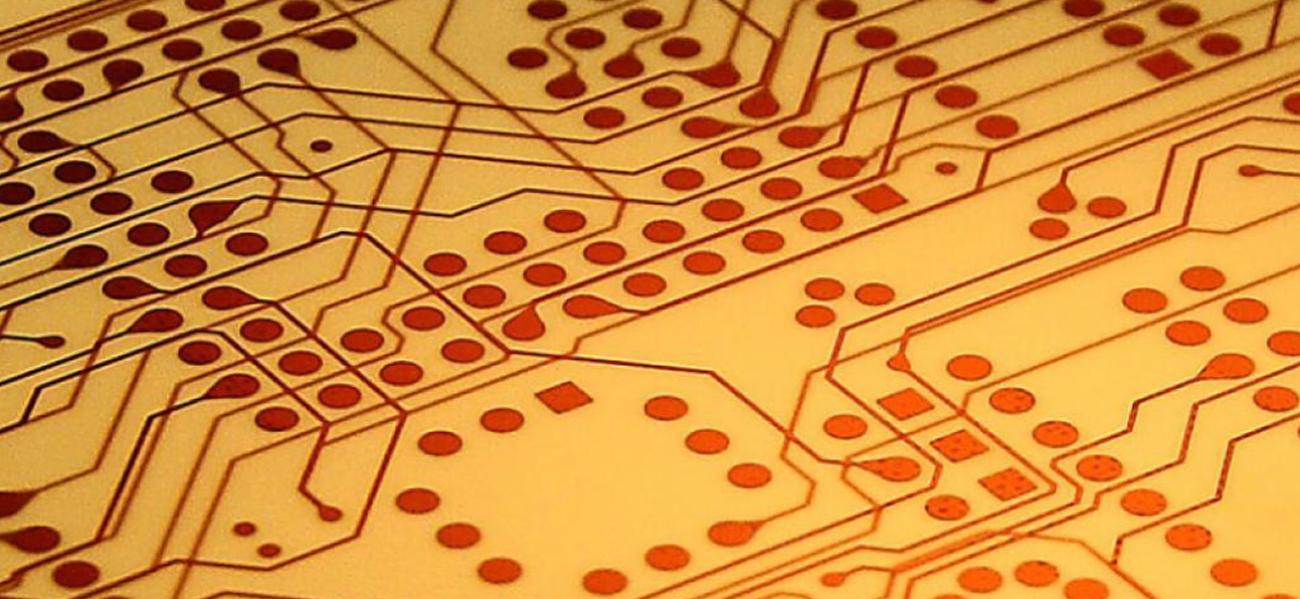
In our last article we described the practices related to Statistical Process Control (SPC).
It was necessary to introduce this topic from the very beginning of this journey through which we will fully describe the manufacturing process of printed circuit boards. As we have already pointed out, in fact, even for standard technology products are requested a lot of production phases, involving the use of no less than 30 different machines and production lines as well as suitable environments for temperature, humidity and cleaning. It is therefore essential to ensure that each production step is stable and under control, otherwise it could entail the production of waste, the generation of extra costs and the consequent reduction in competitiveness, in terms of both, price and delivery times.
The portion of the process following the lamination and photoprinting phases corresponds to the dry film development phase - copper etching – dry-film stripping.
At this stage are performed:
- the developing, i.e. removing, of the dry film not exposed in the photoprint phase and therefore not polymerized
- the etching of the copper not still protected by dry-film after dry-film development so to leave on the panel only the copper corresponding to the tracks provided by the gerber file
- the stripping, i.e. removing, of the dry film which had been kept up till now to protect the tracks.
To optimize the result of this process it is necessary to keep the etching chemistry at precise conditions of "equilibrium" of the various constituents and to keep the temperature stable. The treatment of the pollutions and the resulting sludge is essential for this purpose: the balance must be guaranteed by the combined effect of what is added to the chemistry being etched and what is subtracted at the same time. The entrainment speed of the inner on the belt of the etching line is also important: it must be optimized based on the copper thickness of the inner to be etched.
The table on the next page shows, in particular, the minimum track and/or insulation width allowed as a function of the thickness of the innerlaier base copper.
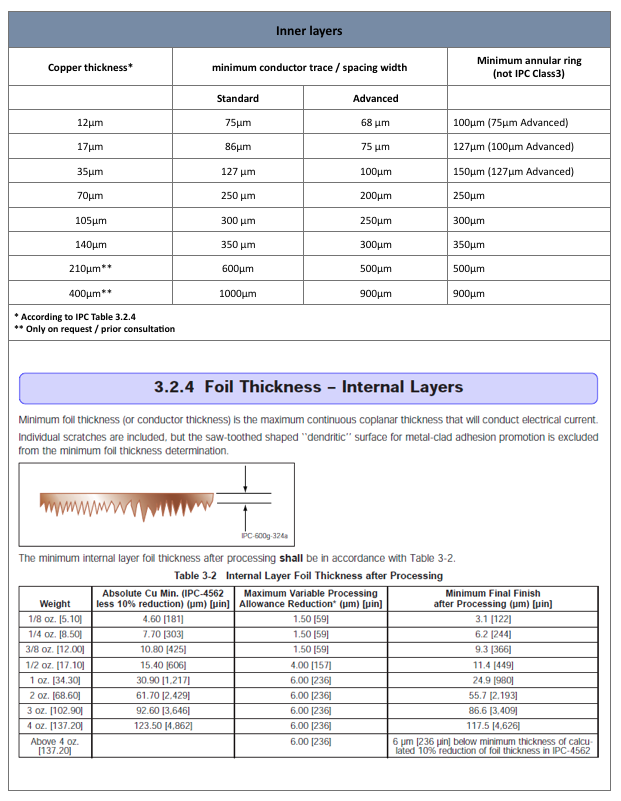
The result of the acid etching process depends not only on the etching process itself but also on the previous ones, the adhesion of the dry-film must be optimized to avoid, for example, under-etching phenomena; during the exposure phase the dry-film must be perfectly clean, the presence of a foreign particle would not allow the dry-film to polymerize correctly in correspondence with this foreign body, thus allowing the dry-film to be removed during the development phase on that “spot” and the underlying copper to be then immediately etched; this would generate an unwanted lack of copper, a so-called “open”.
These are just some of the variables to be guaranteed for the correct development of PBCs production. We will see many others in the continuation of this journey.